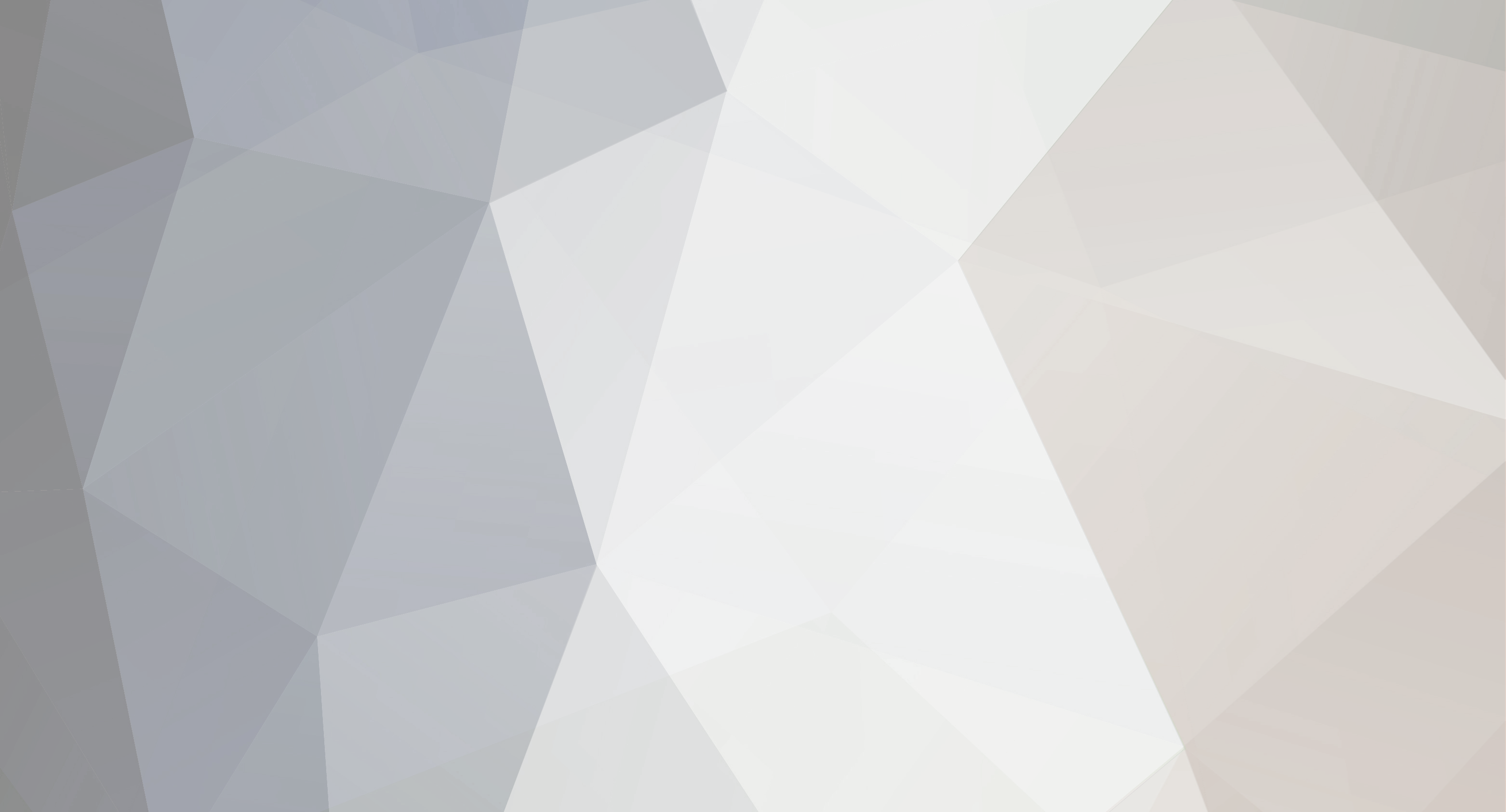
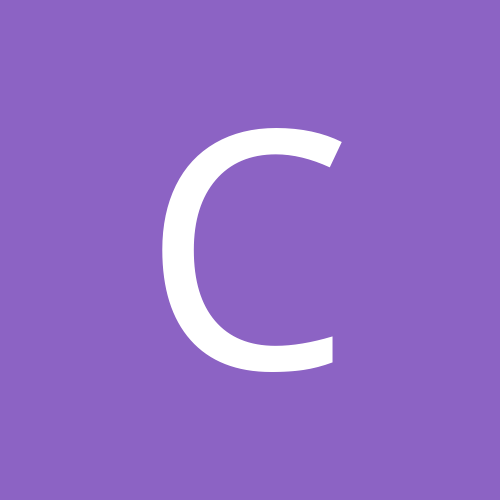
Clevo120Y
-
Content Count
939 -
Joined
-
Last visited
-
Days Won
8
Posts posted by Clevo120Y
-
-
So my above pics are a how not to lesson lol. Sitting in the shed tonight I have come up with another plan, this time I will use ally sheet and make the wind age tray cover the pickup area more, move the gate over etc etc. see how I go tomorrow.
Outback Jack reacted to this -
Thanks Tony, and thanks for the sms's. Tony has pointed out some flaws in my pan which I now agree with, the louvers are the wrong way to work properly so I will have to remake that section
also I will move the front gate to the right as Tony has said so I will remake that piece as well, half a day wasted but hey I learnt something today. Cheers
-
So a bit of an update, the bearings were fine but going to put new shells in anyway, the cam and everything is mickymouse. The valve springs are stuffed, 85lbs on the seat they had reduced to, they are crow single with damper springs, I set them up with 110lbs and that's how soft they went in half a season of racing. So I am taking Tony's advice and setting the head up with the isky 235d springs to sort this problem out for good.
I also started making a sump for this engine, it has to look standard from the outside so all the work is inside, I'm running 2 gates and a bit of a tray and baffles to control the oil. hopefully finish it up tommoz.
started by making so templates
Started cutting it all out and test fitted to a bare block with a pump and pickup in it.
weld some hinges on and clean it up abit, here is also pics of what it will look like when it's all welded together, then I just have to put the trap doors on the hinges and test it out.
-
-
That's some big carbs being used by you blokes, if it works then more power to ya's. What was the drivability like through the rev range with these big carbs?
-
This one just sits on the top of the carb not flush with the housing, I have looked into the other styles and do you think that having the flat surface all the way to the element reduces the element area? My next ones will be radius end all the way over to the outside to allow the whole element to be drawn from and the carb to be able to pull air from below it's top. Just thinking out loud.
-
Hey Tony I have to have flow figures with the manifold and carb bolted on mate, then the average of all 6 cylinders, this is what gives me the VE value.
-
Yeah send it through Tony, I can't touch the head so chamber work is out, I can't zero deck it either, I can take a little bit off but not much, 39thou is not perfect but have to play in the rules
. Cheers Rob yeah the program's make it easier but you still have to know how to interperate the info and balance the figures to something that will work in the real world.
-
The only thing I can't get is the recommended carb cfm, so this will drop overall power, this combination with 4brl manifold and 465 would go really well with a bit of stall.
gerg reacted to this -
A bit of light reading for ya's, this is the engines specs all matched up, this is how I put the details together, once you have the head flow figures with induction on etc etc, then you can start looking into cam profiles that suit intended flow rates with comp and the cross sectional areas that the head has. This is why the combination using mainly stock unbalanced parts can perform well using efficient methods for it's intended rev range which for this engine sits between 3500 and 5500, now to build a sump and make a couple of little changes and go faster this season.
-
249.525 Cubic Inches @ 5500 RPM with 98.33 % Volumetric Efficiency PerCent
Required Intake Flow CFM @28 in. = 165.0 to 174.7 at .548 inch Valve Lift
Required Exhaust Flow CFM @28 in. = 128.8 to 139.6 at .518 inch Valve Lift600 RPM/Sec Dyno Test Lowest Low Average Best
Peak HorsePower 251.3 256.6 259.9 263.2
Peak Torque Lbs-Ft 264.7 271.7 274.6 278.6HorsePower per CID 1.007 1.028 1.042 1.055
Torque per Cubic Inch 1.061 1.089 1.103 1.117
BMEP in psi 160.0 164.2 166.3 168.4
Carb CFM at 1.5 in Hg. 390 434 456 478Recommended Intake Valve Lift to prevent Choke = .548 Lift @ 5500 RPM
Recommended Exhaust Valve Lift to prevent Choke = .518 Lift @ 5500 RPM
Recommended Minimum Normal Maximum Time-Area-Duration Lifts
Intake Valve Lift = 0.4868 0.5483 0.6032 0.6251 0.6589 0.6927
Exhaust Valve Lift = 0.4762 0.5176 0.5694 0.5880 0.6248 0.6616
IntOpen= 9.50 IntClose= 41.50 ExhOpen= 45.50 ExhClose= 5.50
Intake Duration @ .050 = 231.00 Exhaust Duration @ .050 = 231.00
Intake CenterLine = 106.00 Exhaust CenterLine = 110.00
Compression Duration= 138.50 Power Duration = 134.50
OverLap Duration = 15.00 Lobe Separation Angle (LSA)= 108.00
Camshaft Advanced = 2.00 degrees Cylinder Ignition Interval= 120 deg.-- Operating RPM Ranges of various Components --
Best estimate RPM operating range from all Components = 3464 to 5464
Intake Flow CFM @28inches RPM Range from Flow CFM only = 3426 to 5426
Intake and Exhaust Systems operating RPM Range = 3372 to 5372
Intake and Exhaust Time-Area operating RPM Range = 2992 to 4992
Camshaft's Intake and Exhaust Lobes operating RPM range = 3565 to 5565
Intake Valve Curtain Time-Area at 0.550 Lift RPM Range = 3517 to 5517
Exhaust Valve Curtain Time-Area at 0.550 Lift RPM Range = 3844 to 5844Intake Valve Close RPM = 5594 Exhaust Valve Open RPM = 5478
Intake System RPM = 5326 Exhaust System RPM = 5418
Intake Time-Area RPM = 4839 Exhaust Time-Area RPM = 5145
Intake Mach Z-Factor = 0.483911 Exhaust Mach Z-Factor = 0.600718
Intake Z-Factor Lift = 0.554482 Exhaust Z-Factor Lift = 0.500598Curtain Area -to- Valve Area Convergence Intake Valve Lift inch= .450
Curtain Area -to- Valve Area Convergence Exhaust Valve Lift inch= .363Target EGT= 1397.0 degrees F at end of 4 second 600 RPM/Sec Dyno accel. test
Octane (R+M)/2 Method = 91.9 to 94.5 Octane required range
Air Standard Efficiency = 60.51011 % for 9.860:1 Compression Ratio------- Piston Motion Data -------
Average Piston Speed (FPM)= 3584.17 in Feet Per Minute
Maximum Piston Speed (FPM)= 5899.011 occurs at 74.04991 Degrees ATDC
Piston Depth at 74.050 degree ATDC= 1.7059 inches Cylinder Volume= 297.3 CC
Maximum TDC Rod Tension GForce= 2203.0711 G's
Maximum BDC Rod Compression GForce= 1156.4116 G's----- Engine Design Specifications -----
( English Units ) ( per each Valve Sq.Inch area )
Engine Size CID = 249.525 Intake Valve Net Area = 2.472
CID per Cylinder = 41.587 Intake Valve Dia. Area = 2.545
Rod/Stroke Ratio = 1.605 Intake Valve Stem Area = 0.073
Bore/Stroke Ratio = 0.941 Exhaust Valve Net Area = 1.579
Int Valve/Bore Ratio = 0.489 Exhaust Valve Dia. Area = 1.651
Exh Valve/Bore Ratio = 0.394 Exhaust Valve Stem Area = 0.073
Exh/Int Valve Ratio = 0.806 Exh/Int Valve Area Ratio = 0.649
Intake Valve L/D Ratio= .306 Exhaust Valve L/D Ratio= .379
CFM/Sq.Inch = 64.8 to 68.7 CFM/Sq.Inch =76.6 to 80.5Intake Valve Margin CC's Exhaust Valve Margin CC's
1.00 CC = 0.0240 1.00 CC = 0.0370
0.50 CC = 0.0120 0.50 CC = 0.0185
0.25 CC = 0.0060 0.25 CC = 0.0092
0.10 CC = 0.0024 0.10 CC = 0.0037- Induction System Tuned Lengths - ( Cylinder Head Port + Manifold Runner )
1st Harmonic= 36.551 (usually this Length is never used)
2nd Harmonic= 20.745 (some Sprint Engines and Factory OEM's w/Injectors)
3rd Harmonic= 14.483 (ProStock or Comp SheetMetal Intake • best overall HP )
4th Harmonic= 11.399 (Single-plane Intakes , less Peak Torque • good HP )
5th Harmonic= 9.249 (Torque is reduced, even though Tuned Length)
6th Harmonic= 7.781 (Torque is reduced, even though Tuned Length)
7th Harmonic= 6.716 (Torque is greatly reduced, even though Tuned Length)
8th Harmonic= 5.907 (Torque is greatly reduced, even though Tuned Length)
Note> 2nd and 3rd Harmonics typically create the most Peak Torque
4th Harmonic is used to package Induction System underneath HoodPlenum Runner Minimum Recommended Entry Area = 1.760 to 1.980 Sq.Inch
Plenum Runner Average Recommended Entry Area = 2.023 Sq.Inch
Plenum Runner Maximum Recommended Entry Area = 2.067 to 2.446 Sq.InchMinimum Plenum Volume CC = 524.8 ( typically for Single-Plane Intakes )
Minimum Plenum Volume CID= 32.0 ( typically for Single-Plane Intakes )
Maximum Plenum Volume CC = 4089.0 ( typically for Tunnel Ram Intakes )
Maximum Plenum Volume CID= 249.5 ( typically for Tunnel Ram Intakes )--- Cross-Sectional Areas at various Intake Port Velocities (@ 28 in.) ---
127 FPS at Intake Valve Curtain Area= 3.110 sq.in. at .550 Lift
156 FPS at Intake Valve OD Area and at Convergence Lift = .450
192 FPS 90% PerCent Rule Seat-Throat Velocity CSA= 2.061 sq.in.
--- 5500 RPM Intake Cross-sectional areas in Square Inches ---
350 FPS CSA= 1.130 Port has Sonic-Choke with HP Loss ( too fast FPS )
330 FPS CSA= 1.200 Port may have Sonic-Choke with HP Loss ( too fast FPS )
311 FPS CSA= 1.273 Highest useable Port velocity ( possible HP loss )
300 FPS CSA= 1.320 Smallest Port CSA ( Hi Velocity FPS • good TQ and HP )
285 FPS CSA= 1.389 Smallest Port CSA ( very good TQ and HP combination )
260 FPS CSA= 1.523 Recommended average Intake Port CSA (very good TQ and HP)
250 FPS CSA= 1.584 Largest recommended average Intake Port CSA ( good HP )
240 FPS CSA= 1.650 Largest recommended average Intake Port CSA (less Peak TQ)
235 FPS CSA= 1.685 Largest recommended Intake Port Gasket Entry area CSA
225 FPS CSA= 1.760 Largest Intake Port Gasket Entry CSA ( Slow FPS )
215 FPS CSA= 1.842 Possible Torque Loss with Reversion ( Slow FPS )
210 FPS CSA= 1.886 Torque Loss + Reversion possibility ( too slow FPS )
200 FPS CSA= 1.980 Torque Loss + Reversion possibility ( too slow FPS )
Note : these are calculated average Port cross-sectional areas and FPS--- Cross-Sectional Areas at various Exhaust Port Velocities (@ 28 in.) ---
123 FPS at Exhaust Valve Curtain Area= 2.505 sq.in. at .550 Lift
187 FPS at Exhaust Valve OD Area and at Convergence Lift = .363
231 FPS 90% PerCent Rule Seat-Throat Velocity CSA= 1.338 sq.in. at 5500 RPM
--- 5500 RPM Exhaust Cross-sectional areas in Square Inches ---
435 FPS CSA= 0.711 Sonic Choke at Throat Area (too fast FPS velocity)
380 FPS CSA= 0.814 Sonic Choke at Throat Area (possibly too fast FPS)
350 FPS CSA= 0.883 Exhaust Port has Sonic-Choke with HP Loss (too fast)
330 FPS CSA= 0.937 Exhaust Port has Sonic-Choke with HP Loss (too fast)
311 FPS CSA= 0.994 smallest Exhaust Port ( very high velocity FPS )
300 FPS CSA= 1.031 smallest recommended Exhaust Port (Hi velocity)
285 FPS CSA= 1.085 smallest recommended Exhaust Port (Hi velocity)
265 FPS CSA= 1.167 Recommended average Exhaust Port CSA
250 FPS CSA= 1.237 Recommended average Exhaust Port gasket area
240 FPS CSA= 1.288 Recommended largest Exhaust Port gasket area
225 FPS CSA= 1.374 Largest Exhaust Port Exit gasket area (Slow FPS)
210 FPS CSA= 1.473 Largest Exhaust Port Exit gasket area (Slow FPS)
190 FPS CSA= 1.628 Torque Loss + Reversion + Scavenging loss (too slow FPS)
180 FPS CSA= 1.718 Torque Loss + Reversion + Scavenging loss (too slow FPS)
Note : these are calculated average Port cross-sectional areas and FPS -
Your having a go mate and that's all that matters. So whats the next plan, drop an engine off down here and we go to town
slydog reacted to this -
Well the engine got dropped off and now time to make some changes but first a full inspection is in order to make sure it survived the flogging it copped hahaha.
So far the topend is all mickey mouse, I will pull down the bottom end tomorrow and check bearings ect ect.
Had to recheck deck height as I lost my notepad with all the details from last time
-
winton and gerg reacted to this -
well I got my mdf carb top I made back and tested it with the modified carby, soooo close to flowing the same as a stock 350 holley (320cfm).
I'm also about to design and test the same sort of carb tops for these 2 style of carbs, I have dyno testing setup for them when they are ready as well.
gerg reacted to this -
I also think a 465 is the go.
-
I don't think the sumps are interchangeable at all between the 2 engines. Ask Tim (p100ute) he knows the answer because he has looked at it.
Jonathan Mark Davidson reacted to this -
Not yet sorry mate, have been sidetracked with the speedway season about to start up again, the off season went really fast and I have a long list of things to do for a few cars this year
-
So how did the old girl go mate?
-
Yeah I didn't supply or install the springs, the owner did when he got the heads back, the cross sectional area I ported to suit 7400rpm so I was surprised when it fell over earlier, now we know why
-
The XL run down the strip on Wednesday, 11.6 at 114mph, a problem has been discovered, the valve springs that got put in are only 110lbs on the seat which isn't enough for the roller cam, a change of springs is being done soon. We thought the headers were limiting the revs and power it seems to probably be valve float so more power to come from this nasty little 302.
gerg and NZXD reacted to this -
I'm interested in this roller bearing idea Tony, we have to use the XE dizzy in street stock.
-
The theory is sound and works BUT the amount of data needed to get it right is huge. You have just as much chance of finding a suitable single/dual pattern cam profile as finding an off the shelf "scatter" cam that suits your engine.
-
Street Stock Speedway
in Crossflow
Posted
This is my first go at a sump obviously lol, I was actually planning on being able to remove the parts Tony, it's a good idea. I don't know anyone with a nutset so I was just going to rivet it to tabs on the sump instead. I'm running out of time now so a basic sump I will do for now and then spend the time required on a spare sump to add scrapers and shit.